
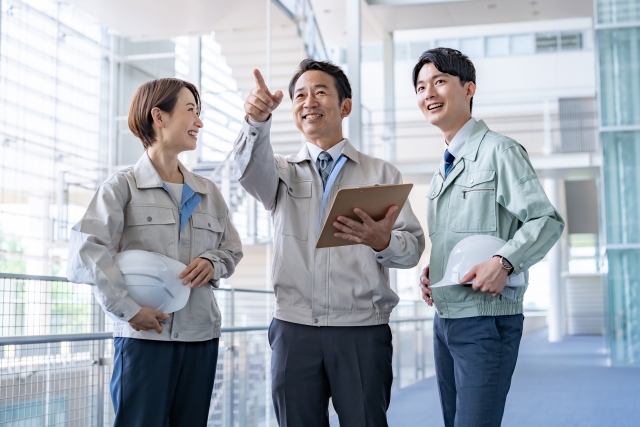
はじめに
皆さんもご存じの通り現在、自動車産業は100年に一度の大変革期を向かえています。
これはEV化に向け軽量化が叫ばれる中、車の構造が大きく変わりそのスピードも想像をはるかに超えて進んでいるからです。
また昨今の自動車メーカーの相次ぐ不祥事により新型車の開発計画が大幅に見直され為に新型車を生産する為の道具(金型や設備)の需要の落ち込みが現実となってきました。
この事から、自動車生産や部品生産をする企業もさることながら、生産をする為の道具(金型や設備)を造る企業も生き残りをかけ、技術革新やリードタイム短縮、徹底した原価低減に取り組まなければなりません。
私は長年プレス技術と金型製作部門で働いてきました。
そこで今回はその経験を生かし金型製作会社や部門の原価低減手法に特化し記事をまとめました。
是非参考にして頂ければ幸いです。
金型原価の把握と改善活動の進め方
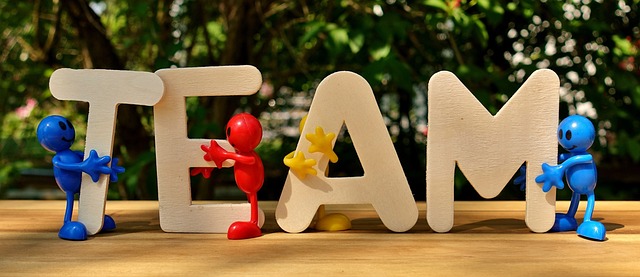
(1)原価改善組織の立ち上げ
会社が儲ける為には売価を上げるか、原価を下げるかですね。
前者は営業部門にお願いする事とし、ここでは全員で取り組む事ができる「原価を下げる」を重点に考えてまいります。
お分かりかと思いますが、社長や部門責任者が社員や部下の皆さんに「何が何でも原価を下げなさい」と根性論や抽象論を言っても何も進みません。
そこでまず、会社一丸となり取り組む為に原価改善組織を立ち上げます。
そして推進責任者と各工程のリーダーを決めます。
下記に原価改善推進組織例を記載します。
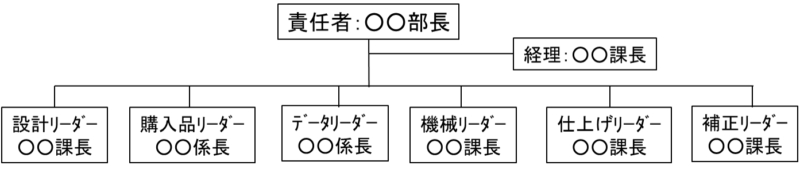
・会社の規模などにより組織を組む事が難しい場合は社長自ら責任者になって下さい。
・上記の例では各リーダーは課長ですが社員育成の為に若手社員を責任者やリーダーに抜擢
しても良いでしょう。
・社長や部門責任者は原価改善活動をスタートする事を必ず全従業員に宣言して下さい。
・推進組織は定期的(最低月1回、出来れば週1回)に原価改善だけに特化した打合せを
行って下さい。そしてその都度PDCAを回して行って下さい。
(2)原価改善活動推進のステップ
推進組織を立ち上げ後は以下のステップで活動を進めて下さい。
① 前年に製作した型の実績原価を把握して下さい。
👇
② 1型当りの目標原価を設定して下さい。(社長及び推進責任者で決定)
👇
③ 次に各工程毎で昨年比、何%原価低減を実施するかを決定しそれを低減必要金額に
置き換えて下さい。(各リーダーが議論し責任者が決定する)
👇
④ 各工程の全員で改善アイテムを抽出して下さい。その場合リーダーはどんな小さな
アイテムでも否定せず実施させて下さい。
(改善アイテムが全てうまく実施出来る保証はないので歩留まりを考慮し改善アイテムを
積み増ししておく事が重要)
👇
⑤ 製作を開始した後は、各工程終了時に原価を把握し目標を達成しているかを
確認して下さい。
(その前に工数・原価が把握できるようシステム化をしておく)
👇
⑥ 目標未達の場合は後工程に改善額を上乗せしてもらいます。例えば型設計工程で目標に
対して10万円オーバーした場合には次の機械加工工程に10万円分改善を積み増しして
もらいます。
(一見、機械加工工程のメンバーは納得出来ないと思うがこれが出来なければ最終的な
目標は達成出来ない)
👇
⑦ 型完成後(客先に売れた)に推進組織全員で反省会を実施し良かった事、良くなかった
事をまとめて下さい。そして良かった事は更に進化させ、良くなかった事は再発防止を
して下さい。
そして改めて改善アイテムを抽出し、次期仕掛り型に改善を織り込んで下さい。
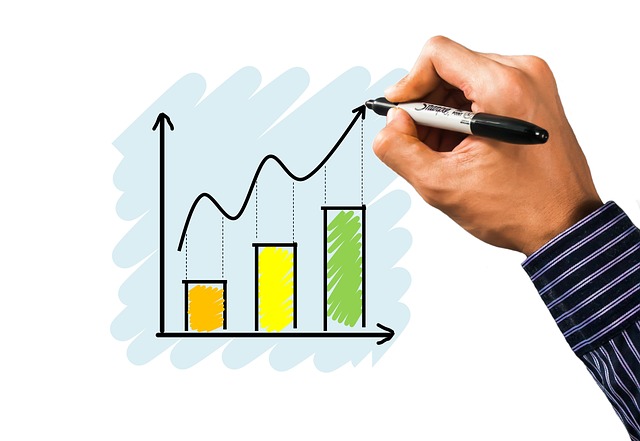
(3)目標と実績の見える化
以下記載のグラフの例のように改善活動の目標や成果が全従業員に見えるようにして下さい。。
① 1型当りの目標のグラフの例
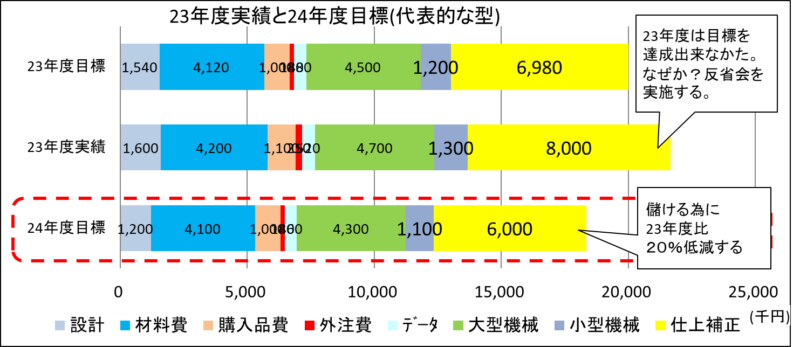
② 各加工工程別の目標のグラフ例
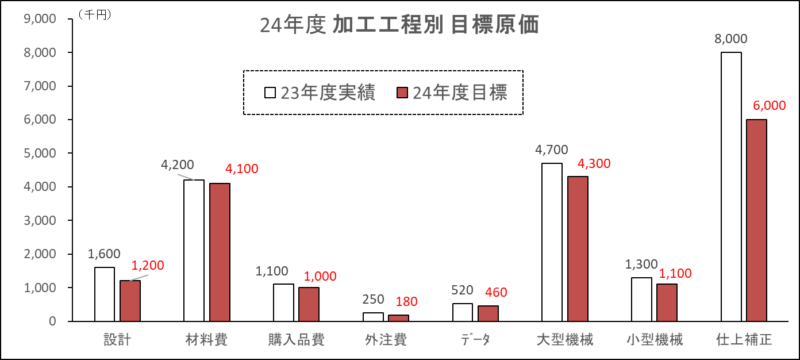
(4)工程別の改善活動の見える化
① 機械工程の例
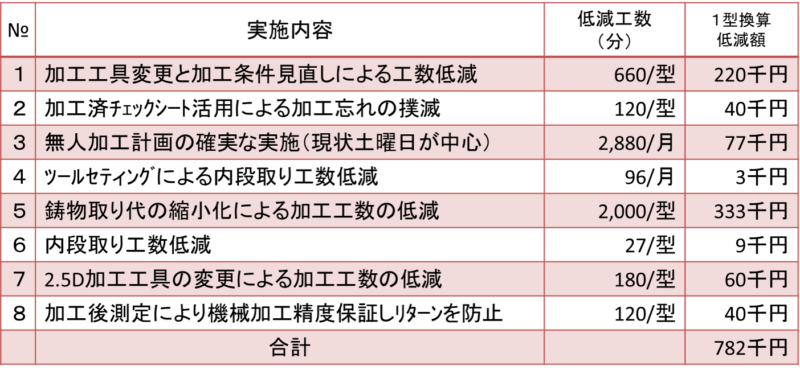
上記の例では歩留まりを考慮し改善アイテムを30%積み増ししています。
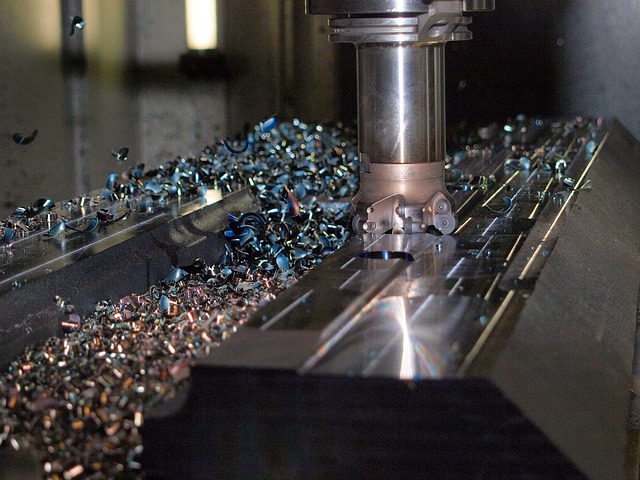
② 購入費の例
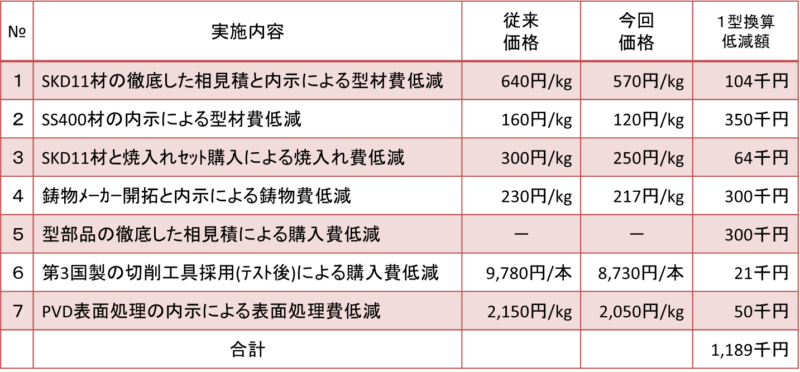
上記と同じように設計工程、仕上げ工程、補正工程の改善アイテムを積み、常に従業員に見えるようにして下さい。。
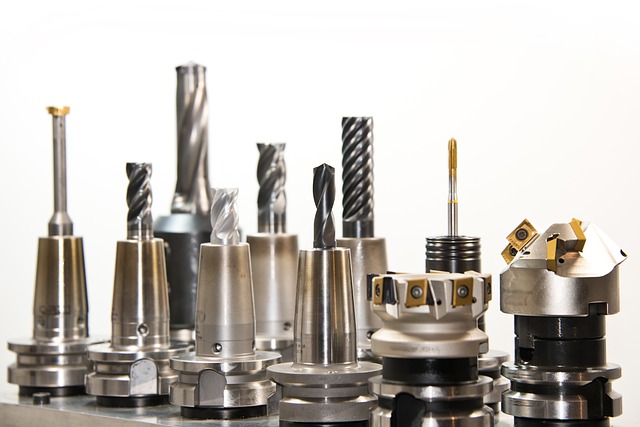
(5)1型当たりの改善活動の見える化
(4)項では加工工程毎の改善アイテムの見える化を説明しましたが、下表のように型毎の
改善アイテムと実績の見える化も重要です。
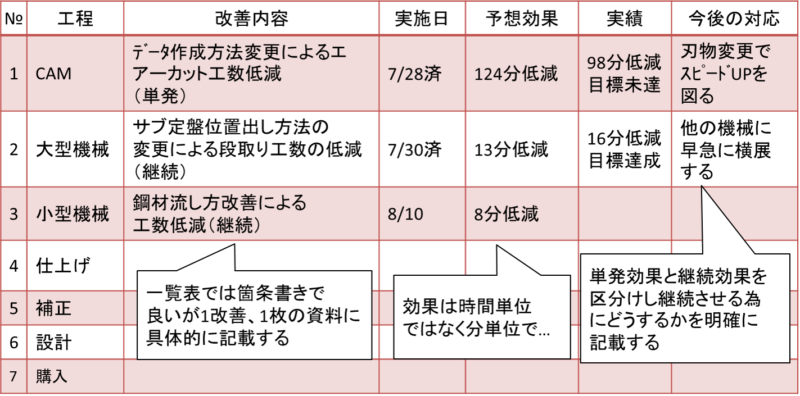
損益分岐点を下げる活動
ここまでは個別型原価の改善活動について説明しましたが、会社全体の費用低減活動も
不可欠です。
費用には固定費と変動費の区分けが有ります。
これらを低減する事で損益分岐点を下げ、利益の出易い体質にする事が必要です。
下図に費用と売上の関係を示します。
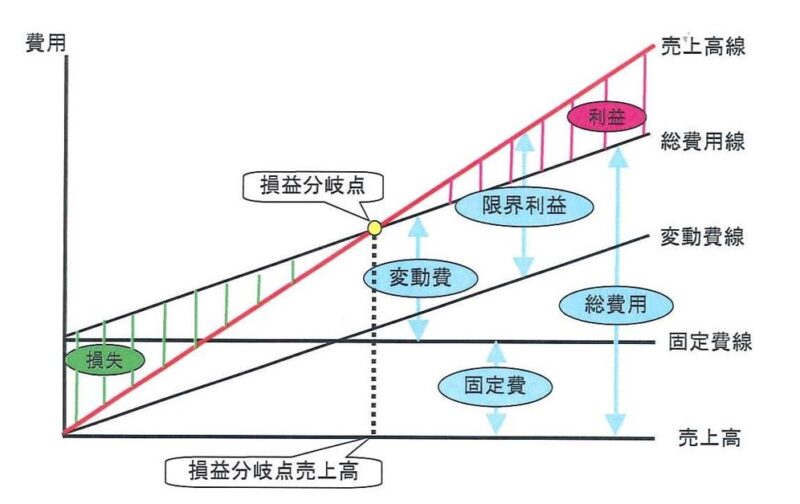
・固定費とは:売上高の増減に関係なく支出される費用
・変動費とは:売上高の増減にほぼ比例して増減する経費
労務費、福利厚生費、減価償却費、賃借料、保険料、修繕料、水道光熱費、旅費、 交通費、
その他製造経費、通信費、消耗品費、広告費、交際費、支払利息、従業員教育費、
研究開発費、その他管理費等
直接材料費、買入部品費、外注費、その他直接経費、運搬費、燃料費、
(製造業では、材料費や外注費は売上高にほぼ比例して計上されるので変動費に分類される。
また、人件費のうち残業代や、残業で発生した電気代などの項目は変動費に分類する。)
鉛筆1本、クリップ1個、こまめなスイッチON・OFに至るまで地道な活動ですが費目毎に
推進リーダーを指名し目標設定、改善アイテムを抽出し月1回程度の進捗報告会を実施すると
良いでしょう。
自社の型製作実力値の把握と対策
企業は利益を上げなければなりません。
利益を求めるがあまり、自社の実力も把握せずにたくさんの型を受注し、日程が守れず客先に
迷惑を掛け、結果として信頼関係が無くなる事は避けなければなりません。
そこで自社の実力を冷静に判断し実力が低ければ対策が必要になります。
① 各工程の工程能力を把握して下さい。
・代表的な型の目標工数を設定して下さい。
・次に前年の各工程の実績工数を把握して下さい。
(ここでの注意点は、やり直し等によりロスした工数を必ず把握して下さい。ロスも
把握せずに「昨年成り行きでこれだけ型製作できたから」と過大に工程能力を評価
してはなりません。)
② ネックとなる工程が解れば改善アイテムを抽出し改善を実施して下さい。
各セクションの工程能力が把握できれば下記の例の通り見える化します、
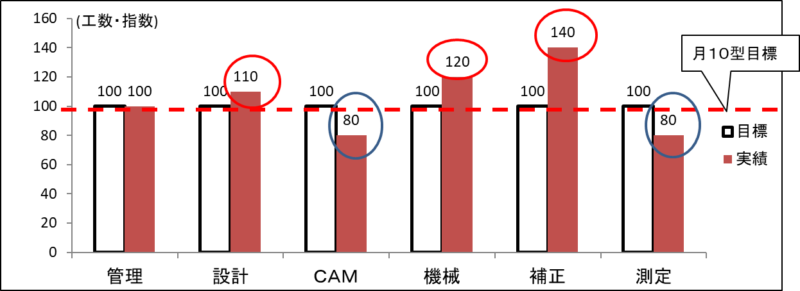
上記の例は設計、機械、補正で工程能力が足りておらず対策が必要となります。
具体的な対策例として
① 工程能力が足りているCAMや測定からの異動。(計画的な多能工化の推進)
② 機械は稼働状況を把握し稼働率を上げる活動や加工改善活動推進。
③ 補正は人員が足りないのか?設計の見込みが悪くやり直しが出ているのか?
機械加工精度が悪いのか?スキルが低くミスが多いのか?など、
要因により打つ手が変わるので冷静に現状を調査し対策を打たなければなりません。
最後に
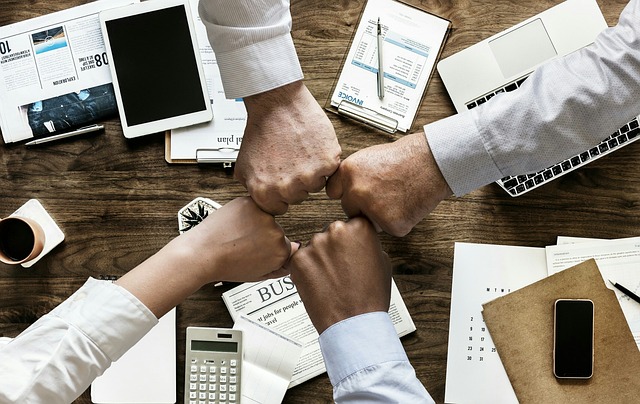
原価改善活動について一般論を説明しましたが会社の特徴や置かれた状況で改善の規模、スピードやどこまでメスを入れるか?が変わってきます。
例えば黒字の会社は、改善活動と同時にお金を使って最新の設備などの投資をする事も考えるでしょう。
一方、赤字続きの会社はお金は使えません。地道な改善も必要だが抜本的な改革が必要です。
しかし如何なる状況においても第一に考えるべきはこれまで協力してくれた従業員だと思います。
常に従業員とコミュニケーションをし、議論をし、経営者と従業員が一枚岩となり改善活動や改革を行う。この事が会社を強くする近道と心得て頂きたいと思います。
トップダウンも必要ですが、そればかりでは従業員は考えようとしなくなり指示待ち人間となってしまいます。
「従業員の皆さんや部下さんはもっと語り合いたいと思っている」
お付き合いいただきありがとうございました。