
にほんブログ村
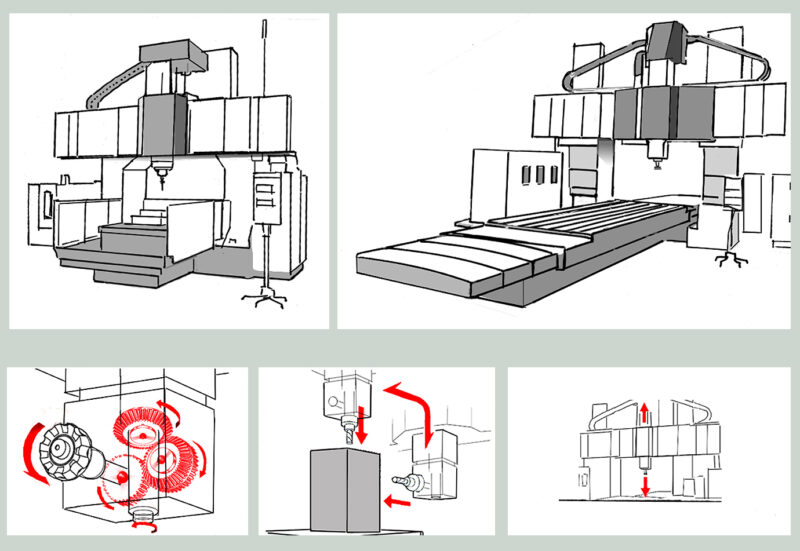
はじめに
ものづくりの会社では保有する生産設備を有効に活用するために稼働率や可動率の指標を用いて改善活動を実施していると思います。
ちなみにトヨタ生産方式では稼働率を「カセドウリツ」、可動率を「ベキドウリツ」と読みます。
一般的な部品製造業での稼働率や可動率の計算方法や活用方法は書籍やネットなどで検索すれば出て来ます。
しかし、部品を生産する為の道具、例えば金型を製作する場合、金型製造業の機械加工工程で使う設備の稼働率や可動率の計算方法や活用方法は検索しても出て来ません。
そこで今回は機械加工工程の設備の稼働率や可動率の計算方法やデータの活用方法を記事に
しました。
金型製作会社や部門の方々の参考になれば幸いです。
*尚、本記事では金型製造業の機械加工工程で使う設備を『工作機械』と表現を統一して使用
します。
部品製造業の稼働率と可動率のおさらい
まず、工作機械の説明の前に一般的な部品製造業の稼働率、可動率についておさらいをしたいと
思います。
「定時での設備フル操業能力に対して必要生産量を造る為に必要な時間の割合」です。
例えば、1日8時間の定時間内で最大8,000個を造れる設備があるとします。
1時間で1,000個造れますね。
その設備で、今日、お客様から、4,000個の受注が有りその数を生産した場合は
4,000(4時間)÷8,000(8時間)×100%で稼働率は50%になります。
またその設備で今日、お客様から、10,000個の受注が有りその数を生産した場合は
10,000(10時間)÷8,000(8時間)×100%で稼働率は125%になります。
お分かりでしょうが、稼働率は受注量に応じて変わります。
従って設備の負荷状況を知り、負荷が高い場合は残業や設備増強の必要性や、負荷が低い場合は設備や人の稼働時間を削減するなどを検討する為に有効なモノサシになります。
「設備を動かしたい時に、正常に動いてくれていた時間の割合」です。
例えば、設備を運転しようとしていた時間が7時間だとします。
実際には設備トラブルや段取り等が発生し設備が止まり、動いていた時間が5時間だった場合は、
5時間÷7時間×100%で可動率は71.4%になります。
設備停止を防ぐために、保全によってもたらされる設備の信頼性を示す指標で常に100%を
目指べきであり、現場が責任を持って向上させるべき重要な指標です。
(設備停止がゼロだったとしても可動率が100%を超える事は有りません)
従って、可動率が100%を大きく下回っている場合は様々な要因で非可動時間が多く、
改善が必要になります。
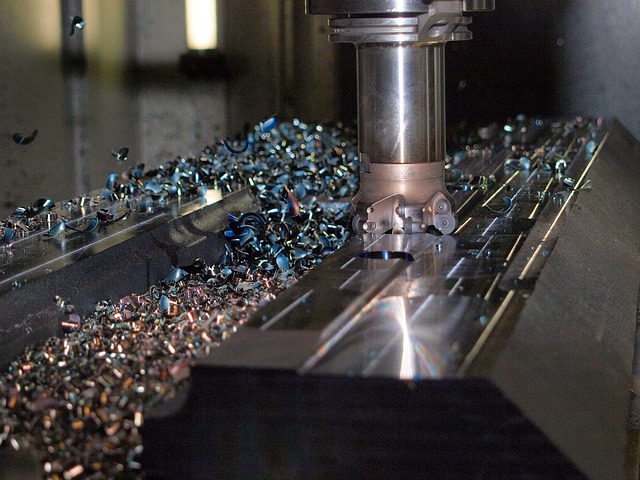
金型製作の工作機械について
(1) 部品生産と金型製作のリードタイム比較
・ まず部品生産のステップは、受注➡プレス➡溶接➡客先納入 です。
リードタイムは約1日と非常に短いです。
・一方、金型製作のステップは、受注➡設計➡機械加工➡仕上げ➡補正➡客先納入 となり
リードタイムは1年以上と非常に長くなります。
(2)金型を製作する工作機械の特徴
・ 機械そのものが高価、また技術革新が早く買い替えサイクルが短い
・ 機械の設置位置が固定され移動が困難
・ ワークの段取に時間と技能が必要
・ 1機械が1工程で作業者は基本的に担当設備に張り付く
以上の事から高価な機械を最大限に動かし、効率よく(早く、正確に、たくさん)金型を加工する事が求められます。
部品製造などでは稼働率を上げても部品が売れなければ在庫になり非効率ですが、金型製造の場合は受注から客先納入まで1年以上かかるので、高価な機械を最大限に動かし(稼働率・可動率を上げて)早く、たくさん、高品質の金型を造る必要があります。
次項からは工作機械の稼働率・可動率の算出方法を説明します。
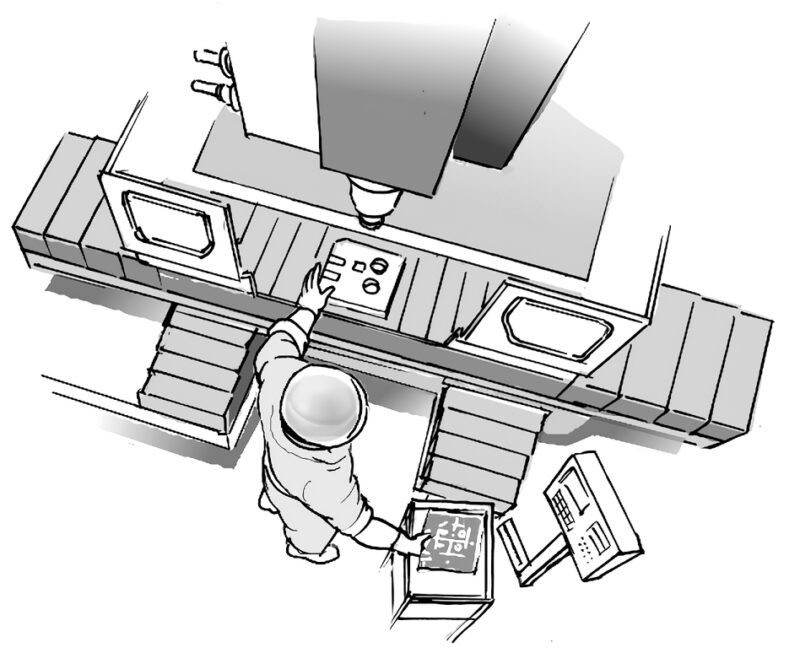
工作機械の稼働率と可動率
稼働率/可動率の算出に当たってのKPI項目を下図に示します。
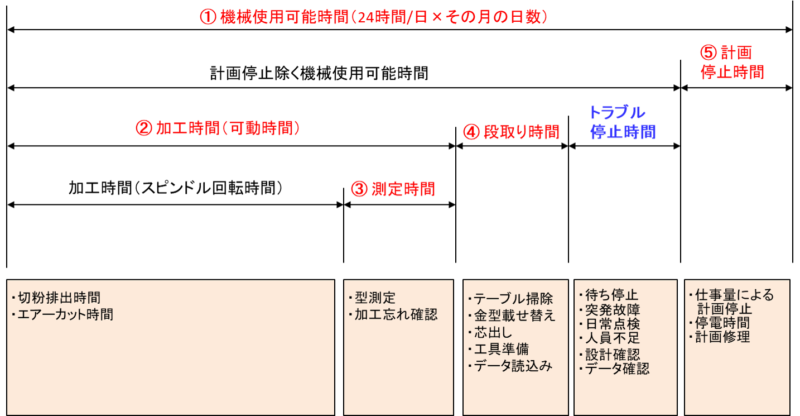
KPI項目を見ながらそれぞれの計算をします。
① 機械使用可能時間=24時間/日×当月の日数
② 加工時間=有人加工時間+無人加工時間
③ 測定時間=加工後のワーク測定時間
④ 段取り時間=テーブル2S/ワーク載せ替え/芯出し時間
稼働率=(②+③+④)÷①×100で求めます。
以下に例を示します。
① 機械使用可能時間=24時間/日×11月の日数(30日)=720時間/月
② 加工時間=450時間/月
③ 測定時間=10時間/月
④ 段取り時間=30時間/月 だったと仮定します。
稼働率=(②450時間+③10時間+④30時間)÷①720時間×100=68.1%
【解説】
100%-68.1%=31.9%の230時間が何等かの要因で機械が止まっていた事になります。
仕事量が多く機械をフル稼働しなければならない場合は、先ずは機械が付加価値を生んでいない230時間の要因を調査し、動かす為に改善を進める必要が有ります。
但し、仕事量が少ない場合は稼働率は必然的に下がりますので一喜一憂する必要は有りません。
① 機械使用可能時間=24時間/日×当月の日数
② 加工時間=有人加工時間+無人加工時間
③ 測定時間=加工後のワーク測定時間
④ 段取り時間=テーブル2S/ワーク載せ替え・芯出し時間
⑤ 計画停止時間=仕事量が少ないための計画停止や停電停止
可動率=((②+③)÷(①-⑤))×100で求めます。
以下に例を示します。
① 機械使用可能時間=24時間/日×11月の日数(30日)=720時間
② 加工時間=450時間
③ 測定時間=10時間
④ 段取り時間=30時間
⑤ 計画停止時間=72時間 だったと仮定します。
可動率=((②450+③10)÷(①720-⑤72 ))×100=71.0% です。
【解説】
可動率の分子には段取り時間は含みません。(稼働率の分子には段取り時間を含みます)
今回の例は仕事量に応じて計画停止を実施したが100%-71.0%=29.0%の188時間が段取りと何等かのトラブルで機械が止まっていた事になります。
従って止まっている時間の要因を調査し加工時間を増やす改善が不可欠です。
(1)項と(2)項で計算した稼働率と可動率の分母・分子の関係を下図に示しましたので参考にして下さい。
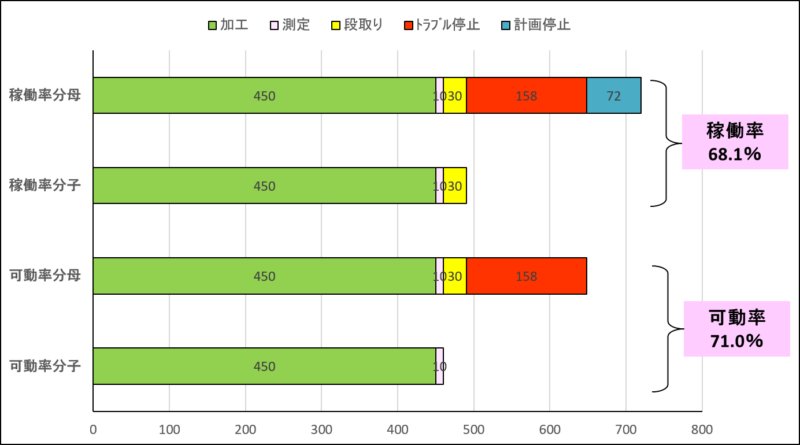
これまでの事から繰り返しになりますが、稼働率は仕事量の多寡に影響されるので数字に一喜一憂する必要は有りません。
重視すべきは可動率です。
可動率はミスや突発故障により機械が停止したり、段取りに時間がかかった場合など異常が発生した場合は低くなります。
異常をなくして可動率を上げる事が望まれます。
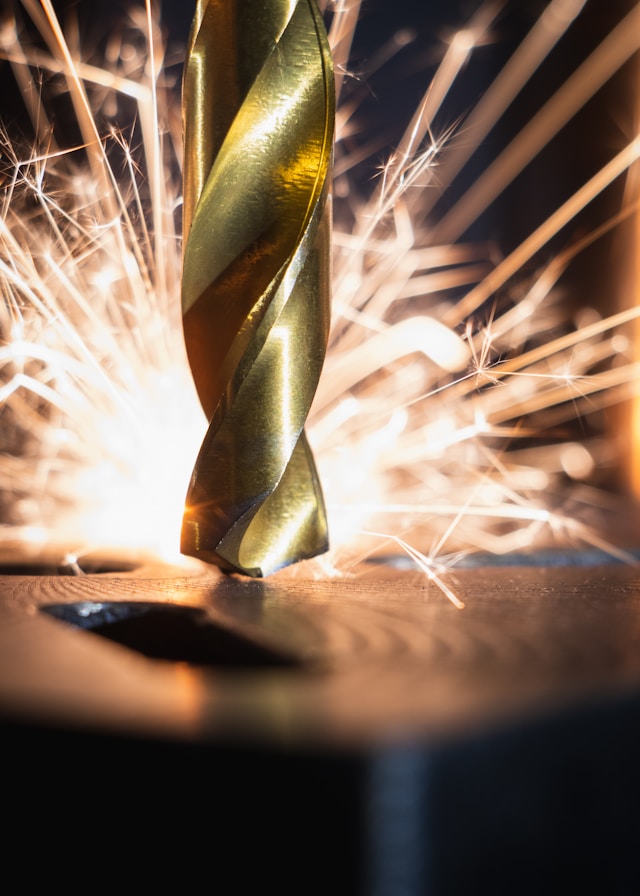
まとめ
稼働率、可動率を見てこなかった会社や部門の皆さんは、先ずはこれまで記載した内容を参考に稼働率と可動率を算出してみて下さい。
一方、すでに数値を把握している皆さんは更に踏み込んで、加工時間の内容を細分化して下さい。
例えば、
・切粉排出時間(スピンドルに負荷がかかっている状態)
・エアーカット時間(スピンドルに負荷がかかってない状態)
などをカウントし、切粉排出時間を増やす活動をして下さい。
また停止時間も内容を細分化して下さい。
例えば、
・設備故障停止時間
・設計ミス、CAMミス、加工ミスによる停止時間や再加工時間
・段取りミスや段取り不慣れによる停止時間
などをカウントし、停止時間を最小限におさえる活動をして下さい。
そして可動率を徐々に上げて、90%以上を目指して下さい。